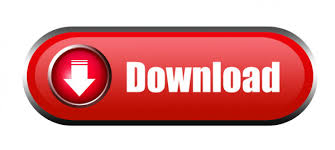

- #Delta orcaview differential pressure pid loop generator
- #Delta orcaview differential pressure pid loop manual
- #Delta orcaview differential pressure pid loop software
Historical trends or process analysis software can be used to identify all the loops on a boiler oscillating with the same period. The loops will all oscillate with the same period of oscillation. The IMC (Lambda) tuning method can be used to obtain very stable control loops and has been proven to help settle down cyclical interactions.īecause a boiler consists of many interactive sub-processes, one oscillating loop can cause several other loops on the boiler to oscillate with it. The simplest technique for solving problems with cyclical interactions is to tune one of the interacting control loops to produce an overdamped response. Cyclical interaction can be aggravated by aggressive tuning, for example when using quarter-amplitude-damping tuning methods, such as the Ziegler-Nichols or Cohen-Coon tuning rules without reducing the calculated controller gain by at least 50%. The pump and valve each affect both the flow and the pressure, and a cyclical interaction between the flow and pressure control loops can easily occur. A good example of this is feedwater flow controlled with a variable-speed pump and differential pressure controlled with a feedwater control valve. Tightly coupled boiler control loops with similar dynamics can begin to oscillate against each other. There are three principal factors that trigger oscillation of boiler control loops: interaction between loops, stiction, and deadband.Ĭyclical Interactions. If it does, troubleshooting should be focused on the main steam temperature controller.
#Delta orcaview differential pressure pid loop manual
To verify this, put the main steam temperature controller in manual and see if the desuperheater outlet temperature controller stops oscillating. For example, if a desuperheater outlet temperature control loop oscillates because its set point is oscillating, the problem likely lies with the main steam temperature controller producing the set point. The cause of oscillations should be traced back to the origin of the loop’s set point. If a control loop’s set point oscillates, it will most likely cause the entire loop to oscillate.
#Delta orcaview differential pressure pid loop generator
For example, steam generator furnace pressure can oscillate because of a partially blocked rotating air heater. Oscillation analysis of interacting loops and equipment should then be done to find the root cause. If the oscillation persists when the controller is in manual mode, the oscillation originates from outside the loop. To narrow down the possible causes of the oscillation, the controller should be put in manual mode to see if the oscillation stops. Oscillations may also be a result of a cyclical interaction between two or more control loops. Oscillations can originate from within the control loop or may be caused by external factors. Other control response problems include sluggish response and noise. Oscillations are cyclical deviations from the set point and often contain a component of randomness. For more information on using performance-monitoring software to improve loop performance, see my earlier article, “Monitoring Control Loop Performance,” in the February 2012 issue, available at. Noise is random movement in the process variable. Sluggish response is a general slowness in the loop’s ability to recover from disturbances or follow set point changes. Oscillations are periodic deviations from set point, frequently intermixed with some random behavior (Figure 1). Common problems and possible causes of poor control performance. Each of these can have several causes (Table 1). Excessive and/or unnecessary deviations from set point can result from oscillations, sluggish control loop response, and excessive measurement noise. Poor control performance makes itself evident primarily when a controlled variable (process variable) deviates excessively from its target value (set point). Tuners can spend many hours trying to tune these challenging control loops, but the loops often remain problematic. These loops may oscillate for seemingly no reason or deviate far from their set points during load ramps and disturbances, often overshooting their set points afterward. Most power plants have a few control loops that never seem to control satisfactorily. Process design certainly plays a role in control loop performance, but experience has shown that the majority of control loops can perform better-provided that the root cause of the poor performance is found and corrected. Only through proper troubleshooting and then solving the underlying problems can control loop performance be improved.
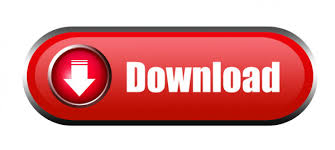